中空吹塑订做需要在产品设计、材料选择、模具制造等多个环节注意细节问题,以确保最终产品符合预期的质量和使用要求。
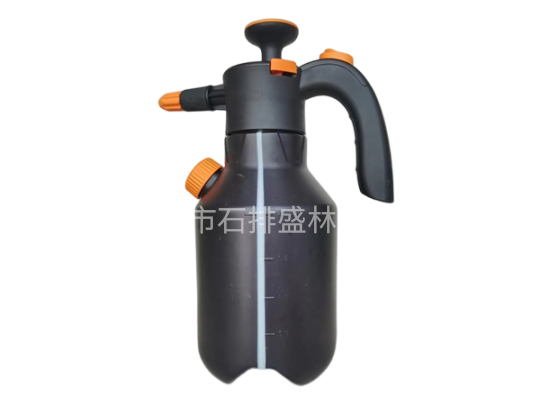
1、产品设计
明确使用需求:需与客户充分沟通,明确产品的用途、使用环境、容纳物特性等,如用于食品包装的容器,要考虑食品卫生标准;用于盛装化学品的容器,要根据化学品的性质选择合适的材料和设计。
合理设计结构:产品的形状、尺寸应便于吹塑成型,避免出现过薄或过厚的区域,防止在吹塑过程中出现局部冷却不均、强度不足等问题。同时,要设计合理的脱模结构,方便产品从模具中取出。
考虑外观要求:根据客户的品牌定位和市场需求,设计出美观、符合市场趋势的外观,包括颜色、表面纹理、标识等元素。
2、材料选择
性能匹配:根据产品的使用要求,选择具有合适物理、化学性能的材料,如要求较高透明度的产品,可选择 PET 等材料;需要良好柔韧性的,可选用 PE 材料。同时,要考虑材料的耐候性、耐温性等,以确保产品在不同环境条件下的稳定性。
质量认证:对于食品、医药等行业的包装产品,所选材料必须符合相应的卫生标准和质量认证要求,如食品接触材料需通过相关的食品安全检测。
成本控制:在满足产品性能要求的前提下,综合考虑材料的成本,选择性价比高的材料,同时,要考虑材料的供应稳定性,避免因材料短缺影响生产进度。
3、模具制造
精度保证:模具的精度直接影响产品的尺寸精度和外观质量,因此要选择有经验、技术实力强的模具制造厂家,采用高精度的加工设备和工艺,确保模具的尺寸偏差控制在允许范围内。
材质选择:根据产品的生产批量和使用要求,选择合适的模具材质。对于大批量生产的产品,应选用耐磨性好、强度高的模具钢,以延长模具的使用寿命,降低生产成本。
维护与保养:要向模具制造厂家了解模具的维护保养要求,制定合理的模具维护计划,定期对模具进行清洁、润滑、调试等保养工作,以保证模具的性能稳定,减少故障发生。
4、生产工艺控制
温度控制:吹塑过程中的温度控制至关重要,包括塑料原料的加热温度、模具的温度等。温度过高可能导致产品变形、表面出现气泡等问题;温度过低则会使产品成型困难,出现裂纹等缺陷。因此,要根据材料的特性和产品的要求,精确控制各环节的温度。
压力控制:压缩空气的压力直接影响产品的成型效果和壁厚分布。压力过小,产品无法充分贴合模具内壁,导致形状不完整或壁厚不均匀;压力过大,则可能造成产品破裂或飞边过大。需要通过试验和调整,确定合适的压力参数。
冷却时间:冷却时间要适当,过短会使产品在脱模后容易变形,过长则会影响生产效率,一般根据产品的尺寸、壁厚和材料的热性能来确定合理的冷却时间,以保证产品具有良好的尺寸稳定性和外观质量。
5、质量检验
外观检查:主要检查产品的表面质量,包括是否有气泡、划痕、裂纹、飞边等缺陷,颜色是否均匀一致,外观是否符合设计要求,对于有印刷或贴标的产品,还要检查印刷质量和标签粘贴的牢固度、位置准确性等。
尺寸精度测量:使用专业的测量工具,如卡尺、千分尺、三坐标测量仪等,对产品的关键尺寸进行测量,确保尺寸偏差在设计要求的公差范围内。
性能测试:根据产品的使用要求,进行相应的性能测试,如产品的强度、密封性、耐冲击性等。例如,对于包装液体的容器,要进行密封测试,确保在运输和储存过程中不会发生泄漏。